Lean manufacturing
De forma resumida puede decirse que Lean consiste en la aplicación sistemática y habitual de un conjunto de técnicas de fabricación que buscan la mejora de los procesos productivos a través de la reducción de todo tipo de “desperdicios”, definidos éstos como los procesos o actividades que usan más recursos de los estrictamente necesarios.
Lean Manufacturing es una filosofía de trabajo, basada en las personas, que define la forma de mejora y optimización de un sistema de producción focalizándose en identificar y eliminar todo tipo de “desperdicios”, definidos éstos como aquellos procesos o actividades que usan más recursos de los estrictamente necesarios. Identifica varios tipos de “desperdicios” que se observan en la producción: sobreproducción, tiempo de espera, transporte, exceso de procesado, inventario, movimiento y defectos.
Su objetivo final es el de generar una nueva CULTURA de la mejora basada en la comunicación y en el trabajo en equipo; para ello es indispensable adaptar el método a cada caso concreto. La filosofía Lean no da nada por sentado y busca continuamente nuevas formas de hacer las cosas de manera más ágil, flexible y económica.
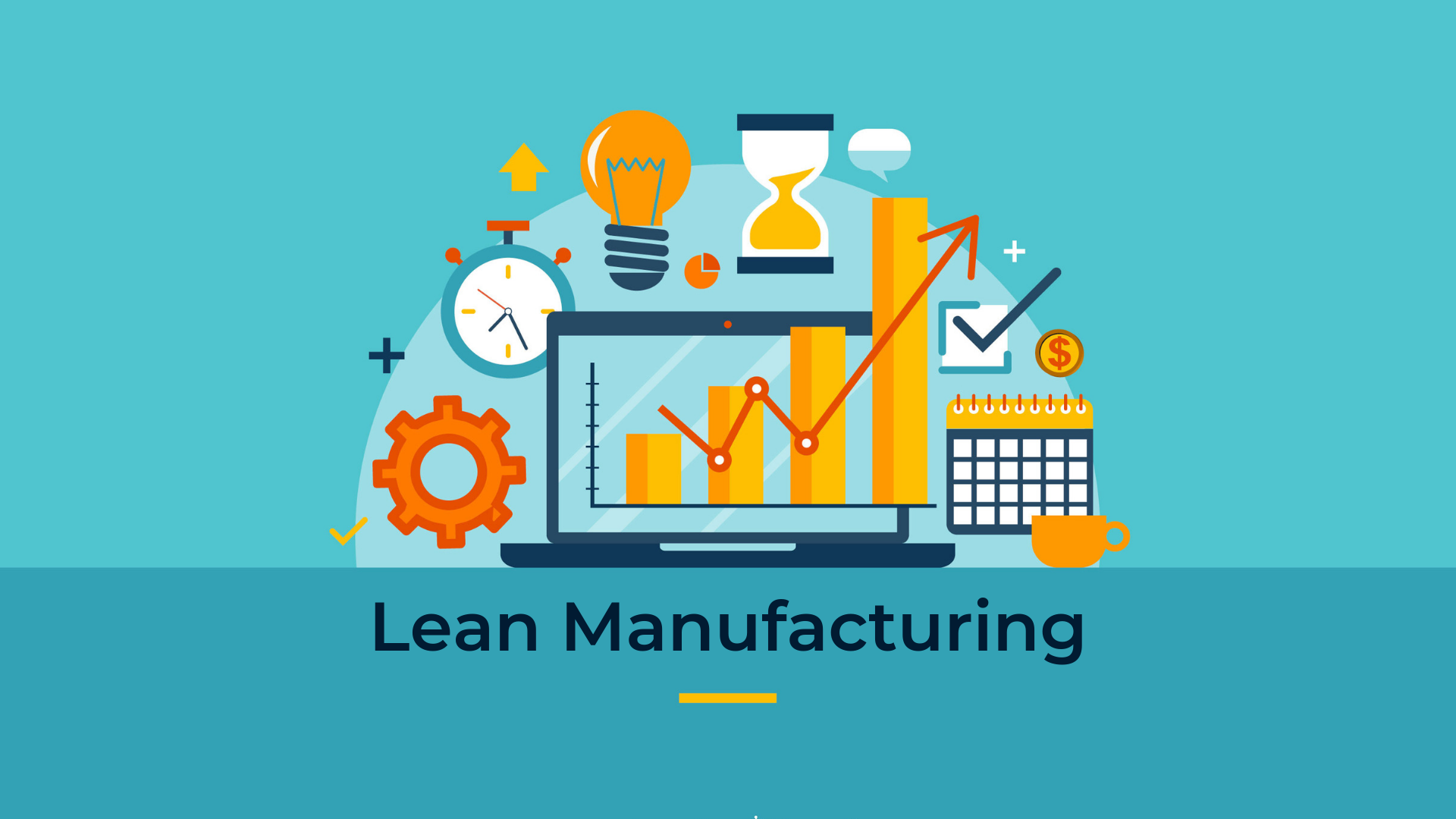
Orígenes y antecedentes
La ruptura con estas técnicas se produce en Japón, en donde se encuentra el primer germen recocido con el pensamiento Lean. Ya en 1902, Sakichi Toyoda, el que más tarde fuera fundador con su hijo Kiichiro de la Corporación Toyota Motor Company, inventó un dispositivo que detenía el telar cuando se rompía el hilo e indicaba con una señal visual al operador que la maquina necesitaba atención. Este sistema de “automatización con un toque humano” permitió separar al hombre la máquina. Con esta simple y efectiva medida un único operario podía controlar varias máquinas, lo que supuso una tremenda mejora de la productividad que dio paso a una preocupación permanente por mejorar los métodos de trabajo
Taiicho Ohno, al que se le considera el padre del Lean Manufacturing, visitaron las empresas automovilísticas americanas. Por aquel entonces el sistema americano propugnaba la reducción de costes fabricando vehículos en grandes cantidades pero limitando el número de modelos. Observaron que el sistema rígido americano no era aplicable a Japón y que el futuro iba a pedir construir automóviles pequeños y modelos variados a bajo coste. Concluyeron que esto solo sería posible suprimiendo los stocks y toda una serie de despilfarros, incluyendo los de aprovechamiento de las capacidades humanas.
A partir de estas reflexiones, Ohno estableció las bases del nuevo sistema de gestión JIT/Just in Time (Justo a tiempo), también conocido como TPS (Toyota Manufacturing System). El sistema formulaba un principio muy simple: “producir solo lo que se demanda y cuando el cliente lo solicita”. Las aportaciones de Ohno se complementaron con los trabajos de Shigeo Shingo, también ingeniero industrial de Toyota, que estudió detalladamente la administración científica de Taylor y teorías de tiempos y movimientos de Gilbreth. Entendió la necesidad de transformar las operaciones productivas en flujos continuos, sin interrupciones, con el fin de proporcionar al cliente únicamente lo que requería, focalizando su interés en la reducción de los tiempos de preparación. Sus primeras aplicaciones se centraron en la reducción radical de los tiempos de cambio de herramientas, creando los fundamentos del sistema SMED. Al amparo de la filosofía JIT fueron desarrollándose diferentes técnicas como el sistema Kanban, Jidoka, Poka–Joke que fueron enriqueciendo el sistema Toyota.
. En este punto hay que destacar que Taicho Ohno ha reconocido que el JIT surgió del esfuerzo por la superación, la mejora de la productividad y, en definitiva, la necesidad de reducir los costes, prueba de que en época de crisis las ideas surgen con más fuerza.
CONCEPTO DE DESPILFARRO VS VALOR AÑADIDO
Lean Manufacturing
propugna un cambio radical cultural. Este cambio consiste en analizar y medir
la eficiencia y productividad de todos los procesos en términos de “valor
añadido” y “despilfarro”.
VALOR AÑADIDO
El valor se añade cuando todas las actividades tienen el único objetivo de
transformar las materias primas del estado en que se han recibido a otro de
superior acabado que algún cliente esté dispuesto a comprar. El valor añadido
es lo que realmente mantiene vivo el negocio y su cuidado y mejora debe ser la
principal ocupación de todo el personal de la cadena productiva.
DESFILFARRO
En este punto, en el entorno Lean se define “despilfarro” como todo
aquello que no añade valor al producto o que no es absolutamente esencial para
fabricarlo. No se debe cometer el error de confundir desperdicio con lo
necesario, es decir, cuando identificamos una operación o proceso como
desperdicio, por no añadir valor, asociamos dicho pensamiento a la necesidad de
su inmediata eliminación y eso nos puede crear confusión y rechazo.
La mejor forma de entender los conceptos descritos y evaluar su magnitud es
identificar algunos de los tipos de despilfarros sobre los que se centra el
Lean Manufacturing; almacenamiento, sobreproducción, tiempo de espera, transporte
o movimientos innecesarios, defectos, rechazos y reprocesos.
1. Despilfarro
por exceso de almacenamiento
El almacenamiento de productos presenta la forma de despilfarro más clara
porque esconde ineficiencias y problemas crónicos hasta el punto que los expertos
han denominado al stock la “raíz de todos los males”.
2. Despilfarro
por “sobreproducción”
El desperdicio por sobreproducción es el resultado de fabricar más cantidad
de la requerida o de invertir o diseñar equipos con mayor capacidad de la
necesaria. La sobreproducción es un desperdicio crítico porque no incita a la
mejora ya que parece que todo funciona correctamente. Además, producir en
exceso significa perder tiempo en fabricar un producto que no se necesita para
nada, lo que representa claramente un consumo inútil de material que a su vez
provoca un incremento de los transportes y del nivel de los almacenes.
3. Despilfarro
por “tiempo de espera”
El desperdicio por tiempo de espera es el tiempo perdido como resultado de
una secuencia de trabajo o un proceso ineficiente.
4. Despilfarro
por “transporte” y “movimientos innecesarios”
El desperdicio por transporte es el resultado de un movimiento o
manipulación de material innecesario. Las máquinas y las líneas de producción
deberían estar lo más cerca posible y los materiales deberían fluir
directamente desde una estación de trabajo a la siguiente sin esperar en colas
de inventario.
5. Despilfarro
por defectos, rechazos y reprocesos
El despilfarro derivado de los errores es uno de los más aceptados en la
industria, aunque significa una gran pérdida de productividad porque incluye el
trabajo extra que debe realizarse como consecuencia de no haber ejecutado
correctamente el proceso productivo la primera vez.
- CONCEPTO DE MEJORA CONTINUA Y KAIZEN
La mejora continua se basa en la lucha
persistente contra el desperdicio. El pilar fundamental para ganar esta batalla
es el trabajo en equipo bajo lo que se ha venido en denominar espíritu Kaizen,
verdadero impulsor del éxito del sistema Lean en Japón.
Kaizen
significa “cambio para mejorar”; deriva de las palabras KAI-cambio y ZEN bueno.
Kaizen es el cambio en la actitud de las personas. Es la actitud hacia la
mejora, hacia la utilización de las capacidades de todo el personal, la que
hace avanzar el sistema hasta llevarlo al éxito.
El espíritu de mejora
continua se refleja en la frase “siempre hay un método mejor” y consiste en un
progreso, paso a paso, con pequeñas innovaciones y mejoras, realizado por todos
los empleados, incluyendo a los directivos, que se van acumulando y que
conducen a una garantía de calidad, una reducción de costes y la entrega al
cliente de la cantidad justa en el plazo fijado
1. Abandonar las
ideas fijas, rechazar el estado actual de las cosas.
2. En lugar de
explicar los que no se puede hacer, reflexionar sobre cómo hacerlo.
3. Realizar inmediatamente las buenas
propuestas de mejora.
4. No buscar la perfección, ganar el 60% desde
ahora.
5. Corregir un error inmediatamente e in situ.
6. Encontrar las
ideas en la dificultad.
7. Buscar la causa
real, plantearse los 5 porqués y buscar la solución.
8. Tener en cuenta
las ideas de diez personas en lugar de esperar la idea genial de una sola.
9. Probar y después
validar.
10. La mejora es
infinita.